Cobalt-chromium alloy is a high-temperature alloy initially used in aerospace materials. Because of its excellent resistance to wear, corrosion and high strength, it is used in large quantities for articulating surface components and load-bearing components of artificial joints.
There are six international standards for cobalt-chromium alloys used in surgical implants, ISO 5832-4, ISO 5832-5, ISO 5832-6, ISO 5832-7, ISO 5832-8, and ISO 5832-12, of which only ISO 5832-4 is a casting standard, while the rest are forged.
Cobalt-chromium alloys can be named and classified according to their chemical composition, for example, ISO 5832-4 and ISO 5832-12 are named cobalt-chromium-molybdenum alloys, indicating that cobalt, chromium and molybdenum are the three components with the highest content, respectively.ASTM F75 uses the name Co-28Cr-6Mo to indicate the content of the main components, which is easy to understand.ISO 5832-6 is named cobalt-nickel-chromium-molybdenum alloy. ASTM F562 uses the name 35Co-35Ni-20Cr-10Mo to indicate that it is good to write out but not good to remember.
Another way to classify cobalt-chromium alloys is by nickel content. ISO 5832-4 and ISO 5832-12 are cobalt-chromium-molybdenum alloys with a nickel content of no more than 1%, while the rest of the cobalt-chromium alloys have a nickel content of more than 9%. The difference in nickel content between the two is more than 10 times.
The density of cobalt-chromium-molybdenum alloy is 8.4g/cm3, which is heavier than ordinary stainless steel and nearly twice as heavy as titanium.
Cobalt-chromium-molybdenum alloys have a modulus of elasticity of about 220 GPa, which is slightly higher than that of stainless steel, more than twice as high as that of titanium alloys, and about 10 times higher than that of cortical bone. The stress masking effect is more severe with cobalt-chromium-molybdenum than with titanium alloys for the same part.
ISO 5832-4 is a cast cobalt-chromium-molybdenum alloy. The method of investment casting is usually used. Precision casting can obtain a more complex shape, the size of the more accurate parts, such as femoral condyles, tibial platform, femoral stem and mortise cup.
Cast cobalt-chromium-molybdenum alloys are insensitive to cracking and have high strength. The yield strength is 665 MPa.
GB 4234.4 is equivalent to ISO 5832-4, and YY 0117.3 is the casting standard corresponding to it. ASTM F75 is the corresponding American standard, and the chemical composition is very close to ISO 5832-4, but not exactly equivalent.
The International Standard ISO 5832-4 has no requirements for the metallographic organisation of cast cobalt-molybdenum-chromium gold. The other five International Standards for wrought cobalt-chromium alloys have requirements for the metallographic organisation.
Cobalt and chromium are the two basic elements of cobalt-based alloys, while the addition of molybdenum results in finer grains and higher strength after casting or forging.
ISO 5832-12 is a forged cobalt-chromium-molybdenum alloy. Its yield strength is much higher than that of cast cobalt chromium molybdenum, greater than or equal to 897 MPa. The forging and forming properties of forged cobalt chromium molybdenum alloy are actually not too good, and in the annealed condition, its elongation at break is 20%, which is the lowest compared with other forged cobalt chromium alloys. In the international standard, forged cobalt-chromium-molybdenum than cast cobalt-chromium-molybdenum more than 0.25% of nitrogen, is to improve its forging performance.
YY 0605.12 is equivalent to ISO 5832-12, ASTM F1537 is the corresponding American standard, and ASTM F799 is the standard for forgings of the same material.
Forged cobalt-chromium-molybdenum alloys are sometimes used in the manufacture of femoral shanks, predominantly for cemented shanks, but also individually for uncemented shanks. Because titanium alloys have half the modulus of elasticity of cobalt-chromium-molybdenum, less stress-masking effect than cobalt-chromium-molybdenum, and are less expensive than cobalt-chromium-molybdenum, titanium alloys are used in the majority of uncemented femoral shanks.
Forged cobalt-chromium-molybdenum alloys are also seldom used for the manufacture of femoral condyles because they are more complex in shape and more economical to cast. When forging is used, excess material must be removed by machining, which is time-consuming, costly and uneconomical.
The occasion where forged cobalt-chromium-molybdenum alloys are heavily employed is in the manufacture of femoral heads.
Since cast and forged cobalt-chromium-molybdenum alloys have very good wear properties and a nickel content that is 10 times lower than that of other cobalt-chromium alloys, nickel allergy can be effectively avoided. Therefore, cobalt-chromium-molybdenum alloys are preferentially used for articulating surface components, such as femoral heads and femoral condyles, and account for the lion’s share of the total cobalt-chromium alloys used.
Other forged cobalt-chromium alloys have good deformation properties, suitable for hot and cold deformation processing, can be used for processing a variety of wires, tapes, plates, tubes and so on. This kind of forging cobalt-chromium alloy with high nickel content is generally not used for articulating surface parts.
Table 1 lists all the international, national or industry standards for cobalt chromium alloys for surgical implants, as well as all the ASTM standards. Different types of cobalt chromium alloys are distinguished by different colours. As can be seen from the table, the ASTM standard prefers to develop the material standard and the profile standard separately into different standard numbers.
Table 2 shows a comparison of the chemical composition of these standards
Table 3 lists the comparison of physical and mechanical properties of cobalt-chromium alloys in different standards;
Table 1 Overview of cobalt-chromium alloy standards
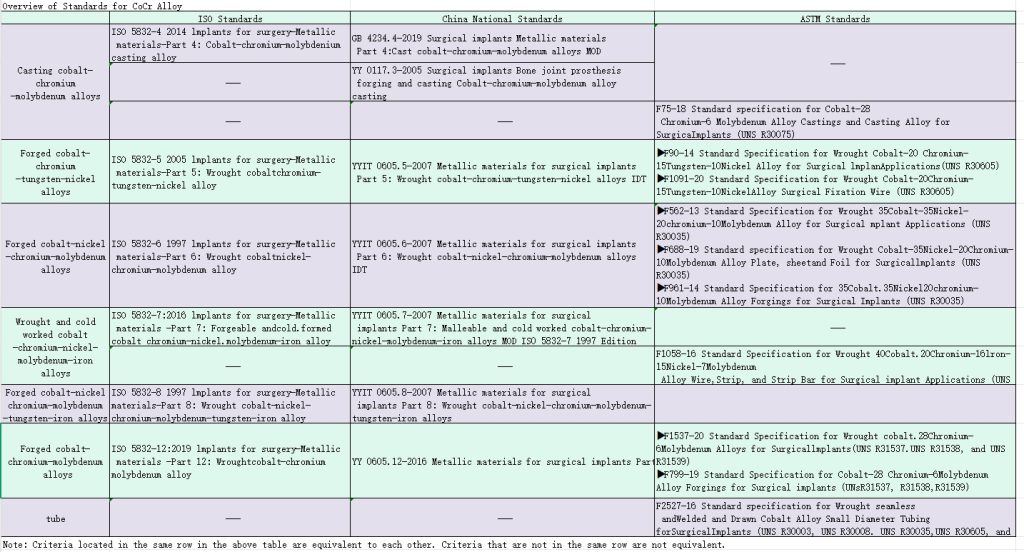
Table 2 Comparison of chemical composition of cobalt-chromium alloys
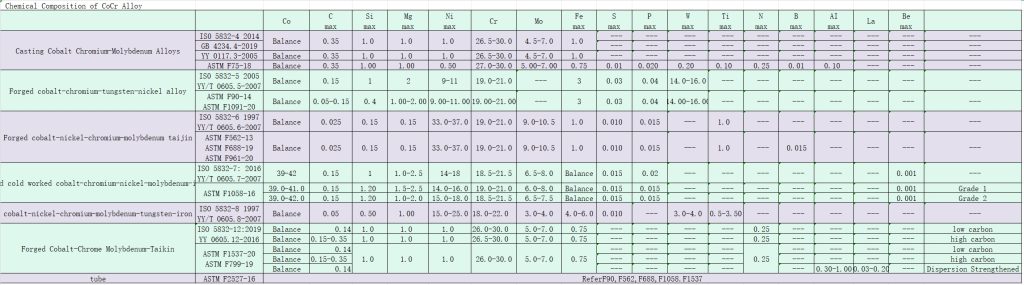
Table 3 Comparison of mechanical and physical properties of cobalt-chromium alloys in different standards
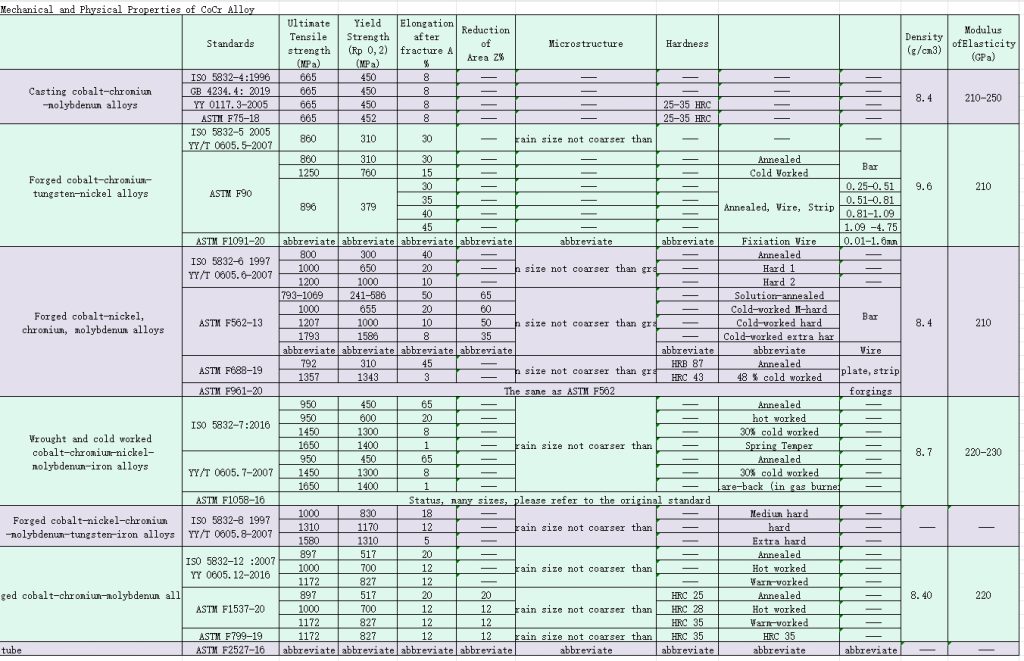