Titanium alloy strength is relatively high, yield strength is greater than 760MPa, about 1.8 times the annealed high nitrogen stainless steel, also greater than the yield strength of medium hardness high nitrogen stainless steel. It is suitable for making parts with large bearing capacity, such as joint handles.
Titanium alloy is sensitive to surface cracks, when used in joint handles, the surface of the parts subjected to large forces is required to be smooth, because tiny scratches or even laser engraving may become a source of fatigue cracks, so there shall be no scratches or laser engraving in the parts subjected to large forces.
Titanium alloys are not wear-resistant and are not suitable for articulating surface components such as ball heads, single-stage heads, bipolar head cups and femoral condyle components of the knee, unless they have undergone a special surface treatment.The appendices of ISO 21534 and YY 0118 as well as YY 0502 explicitly state that titanium and titanium alloys should not be used for articulating surface components.
The density of titanium alloy is 4.4~4.5, which is more than half of that of stainless steel or cobalt-chromium-molybdenum.
Titanium alloys have a modulus of elasticity of approximately 114 GPa, which is close to that of pure titanium, half that of stainless steel or cobalt-chromium-molybdenum, and approximately five times that of cortical bone. Therefore, titanium alloys have a smaller stress-masking effect than stainless steel or cobalt-chromium-molybdenum.
Titanium is a non-magnetic material
Titanium and titanium alloys are not only in the molten state, even at high temperatures above 400 ℃ solid state is also very susceptible to air, moisture, grease, oxide skin and other contamination, and absorption of oxygen, nitrogen, hydrogen, carbon and other elements, so that the welded parts of the plasticity and impact toughness decline, and prone to cause porosity. The gas that produces porosity is hydrogen. Because the solubility of hydrogen in titanium decreases with increasing temperature, welding along the fusion line near the heating temperature is high, it will cause hydrogen precipitation, so pores are often formed near the fusion line.
Titanium and titanium alloy compared with other metals, has a high melting point, heat capacity is small, thermal conductivity is small. Therefore, the weld is easy to produce overheating organisation, grain growth coarse, easy to cause plasticity reduction. Dissolved in titanium in the hydrogen at 320 ℃ and titanium will send the main eutectic transition, precipitation TiH2, caused by the decline in metal plasticity and impact toughness, at the same time produce volume expansion and cause greater stress, which can lead to serious cold cracks.
Therefore titanium implants, especially those subjected to high forces, such as articulating stems, should not be used for removing surface defects by filler welding.
Titanium alloys for surgical implants are mainly classified as Ti6Al4V and Ti6Al7Nb. Among them, Ti6Al4V is further divided into two categories, non-ELI and ELI. ELI is the abbreviation of extra low interstitial, which stands for its ultra-low interstitial impurity content.
Table 1 lists all the international, national or industry standards, as well as the American ASTM standards, for titanium alloys for surgical implants. Different types of titanium alloys are distinguished by different colours. As can be seen from the table, the ASTM standard has four more types of titanium alloys than the ISO standard and the YY/GB standard, which are listed at the end.
A comparison of the chemical composition of these standards is presented in Table 2.
Table 3.1 lists the comparison of physical and mechanical properties of Ti6Al4V in different standards.
Table 3.2 lists the comparison of the physical and mechanical properties of Ti6Al4VELI in different standards; there is no specific ELI in the ISO standard, and there are ELI and non-ELI in GB and ASTM. For example, in GB/T 13810, ELI has lower impurity elements, and thus the yield strength and fracture strength are lower than those of non-ELI.ASTM also has the same law.
Table 3.3 lists the physical and mechanical properties of Ti6Al7Nb in different standards and a comparison of the physical and mechanical properties of titanium alloy forgings and castings in different standards.
For forgings, YY 0117.1 is only a standard for Ti6Al4V forgings, and its counterpart, ASTM F620, covers Ti6Al4V and Ti6Al7Nb, as well as forgings of other types of titanium alloys.
For castings, YY 0117.2 and ASTM F1108 are both casting standards for Ti6Al4V and do not cover Ti6A7Nb and other titanium alloys.
GB/T 13810 is a very comprehensive standard that covers both pure titanium, pure titanium ELI, and in titanium alloys Ti6Al4V, Ti6Al4VELI, and Ti6Al7Nb. That is to say, it contains all the pure titanium and titanium alloys in the ISO 5832 series of standards. However, the mandatory hydrogen content of GB/T 13810 of not more than 0.008% significantly reduces its chances of adoption. Because ISO 5832 series standard is the material standard approved in YY 0118 and YY 0502, in which the hydrogen content is allowed to be up to 0.015%, which is much wider than the requirement of GB/T 13810. This makes the raw material price lower. Since it is widely used, the adoption is high, which further reduces the material cost and shortens the delivery cycle, forming a positive cycle. On the other hand, pure titanium and titanium alloys in the ISO 5832 series have been used clinically for more than 30 years, and are proven safe materials in terms of product strength, biocompatibility and safety considerations. Excessive tightening of the hydrogen content will result in GB/T 13810 not being prioritised, and thus being marginalised.
Table 1 Overview of Titanium Alloy Standards
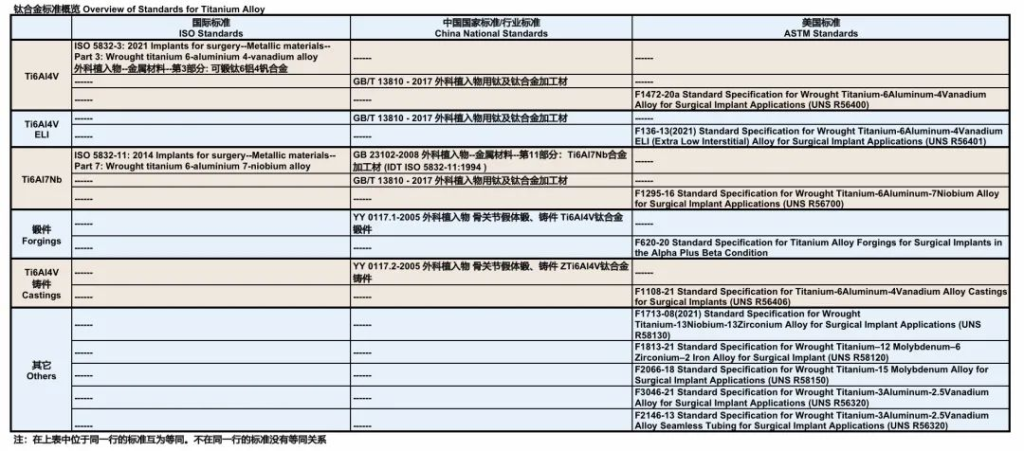
Table 2 Comparison of chemical composition of titanium alloys
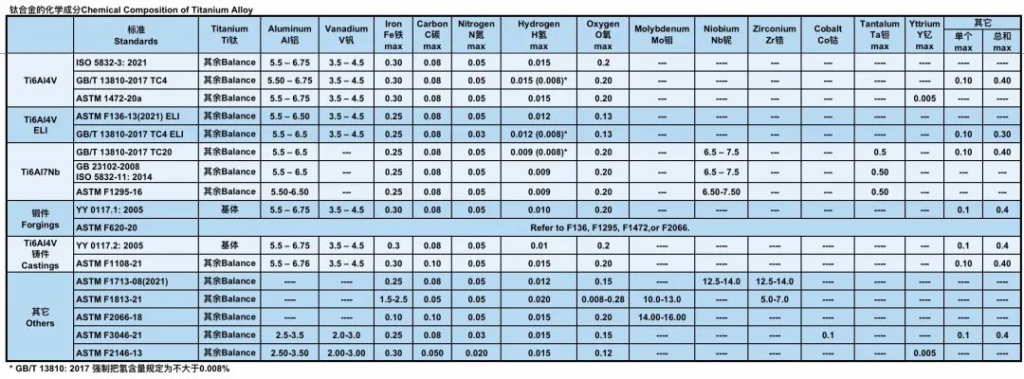
Table 3.1
Comparison of mechanical and physical properties of Ti6Al4V in different
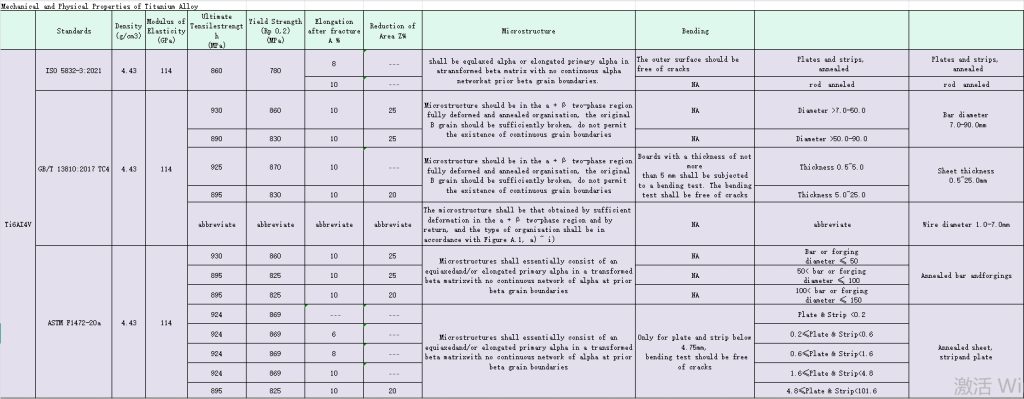
Table 3.2
Comparison of mechanical and physical properties of Ti6Al4VELI in different standards
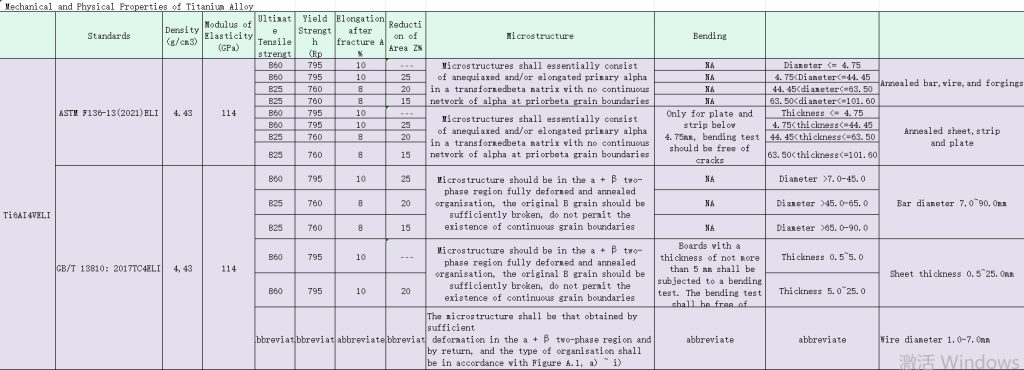
Table 3.3
Comparison of mechanical and physical properties of Ti6Al7Nb, and titanium alloy forgings and castings in different standards
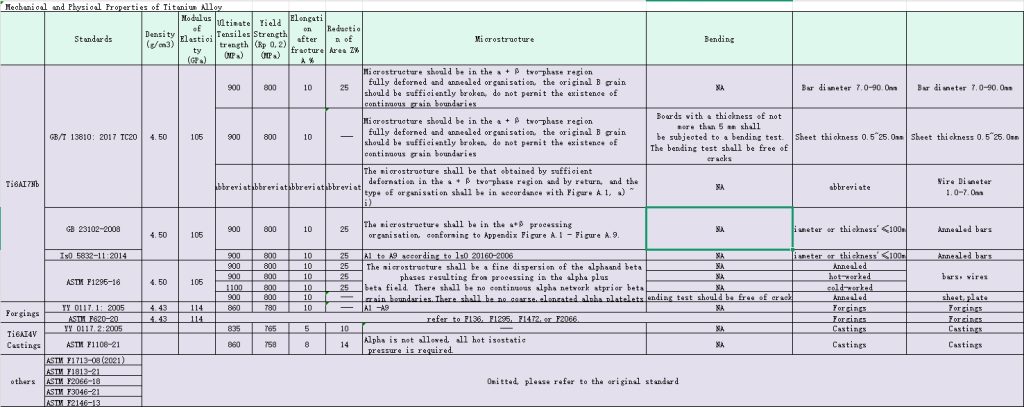