I. Preparation of raw materials
The raw materials for TC23 titanium alloys usually include high purity titanium sponge and other alloying elements such as aluminium and vanadium. The quality of these raw materials directly affects the performance of the final product, so their purity and chemical composition must be strictly controlled.
II. Melting technology
Vacuum arc melting: Vacuum arc melting is one of the melting methods commonly used to produce TC23 titanium alloy. Under the vacuum environment, the high temperature of the electric arc is used to melt the raw materials, and the alloy components are evenly mixed by electromagnetic stirring and other means. This method can effectively avoid oxidation and impurity contamination, and improve the purity and quality of the alloy.
Electron beam melting: Electron beam melting technology is also an advanced melting method, which uses the high temperature generated by the high-speed impact of the electron beam to melt the raw materials. This method has the advantages of concentrated energy, fast heating speed, precise temperature control, etc. It is suitable for melting of high melting point and high purity materials.
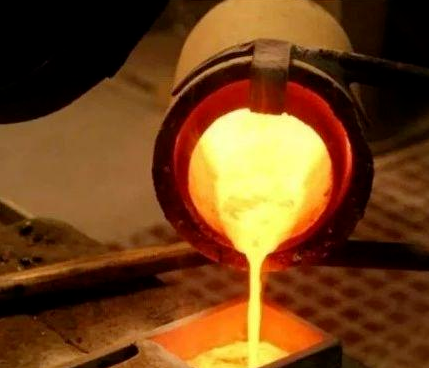
III. Forging technology
Forging of TC23 titanium alloy is an important part of its processing. During the forging process, the forging temperature, forging speed and forging ratio need to be strictly controlled to ensure that the organisation and properties of the alloy meet the requirements.
Heating temperature: the heating temperature of the forging blank should be higher than the beginning of the forging temperature, generally controlled within a certain range (such as 1130 ~ 1180 ° C), in order to avoid cracks and deformation in the forging process.
Forging equipment: the use of advanced forging equipment, such as hydraulic presses, hammer forging machine, etc., in order to improve the precision and efficiency of forging.
Forging process: according to the shape and size of the forgings, choose the appropriate forging process, such as free forging, die forging and so on. In the forging process, it is also necessary to pay attention to the control of forging deformation to avoid excessive residual stress.
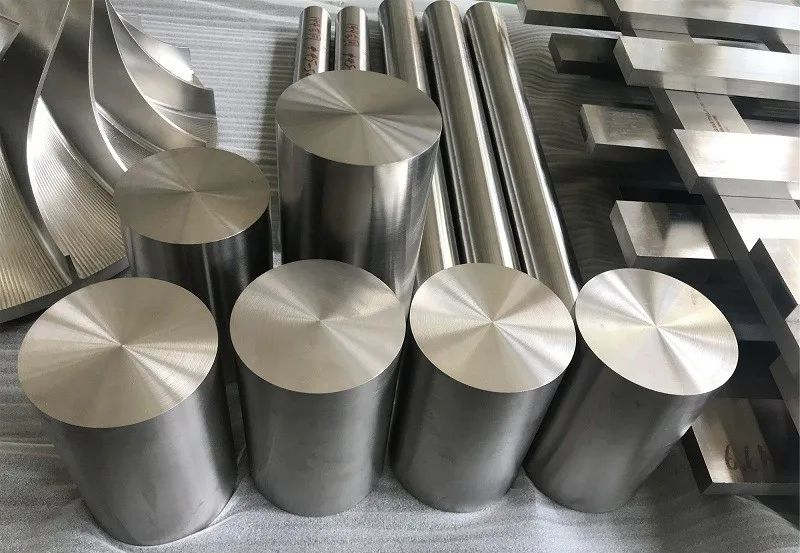
IV. Heat treatment technology
Heat treatment is an important means to improve the properties of TC23 titanium alloy. Through solution treatment, aging treatment and other heat treatment processes, the residual stress in the alloy can be eliminated, grain refinement, improve strength and toughness.
Solid solution treatment: the alloy is heated to a certain temperature (usually higher than the phase transition point), held for a certain period of time after rapid cooling to obtain a uniform single-phase organisation.
Ageing treatment: In the alloy after solid solution treatment, by controlling the heating temperature and time, the reinforcing phases (e.g. Ti3Al, TiAl, etc.) in the alloy are precipitated and uniformly distributed, so as to improve the strength and toughness of the alloy.
V. Precision machining technology
Precision machining of TC23 titanium alloy includes cutting, grinding, polishing and other processes. Precision machining is difficult due to the high hardness of titanium alloy, low thermal conductivity and easy chemical reaction with cutting tools. In order to improve machining efficiency and quality, the following methods can be used:
Optimise cutting parameters: choose suitable parameters such as cutting speed, feed and depth of cut to reduce cutting force and frictional resistance.
Adoption of advanced processing technology: advanced technology such as high-speed cutting, ultrasonic processing and laser processing can effectively reduce the difficulty of processing and improve processing accuracy.
Cutting tool design and coating: develop special cutting tools suitable for titanium alloy machining, and improve tool wear resistance and reduce cutting force through surface coating technology.
In summary, the processing technology of TC23 titanium alloy involves many aspects, and it is necessary to strictly control the process parameters and quality requirements of each link to ensure that the performance and quality of the final product meet the requirements.
- Volume and intensity of physical activity and incidence of cardiovascular disease
- Exclusive | How to Design a Reliable, Low-Energy, Wearable Medical Syringe
- Materials Circle | Ten Properties and three special functions
- Robot-assisted transcatheter mitral valve replacement completed in first case
- Advances in materials and devices for interventional embolization therapy