Ultrasonic fatigue test, using piezoelectric and magnetostrictive principles, converts a voltage signal with a frequency of 20kHz into a high-frequency mechanical vibration. It can be applied to the ultra-high frequency fatigue performance test and research of metal materials. The macroscopic morphology of the complete specimen of this test is shown in Fig. 1.

Figure 1
Ultrasonic fatigue fracture low magnification morphology
The low magnification morphology of the fracture under the scanning electron microscope is shown in Fig. 2, which shows that the fracture source (the lower edge of the section), the extension area (the lower half of the section) and the instantaneous fracture area (the upper half of the specimen) are relatively distinct. The fracture is flush, without obvious necking and deformation.
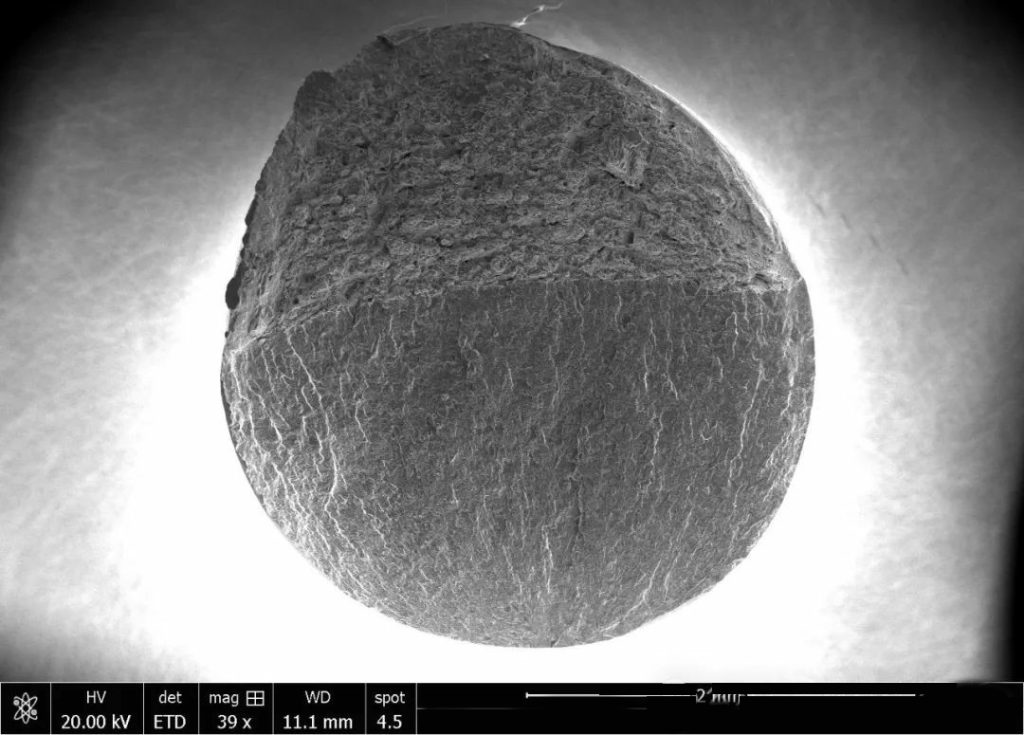
Figure 2
source of fracture
The fracture originated at the lower edge of Figure 2. The magnification is shown in Figure 3. inclusions are present in this area. Fatigue sources often sprout from weak areas in the specimen such as inclusions and cracks.
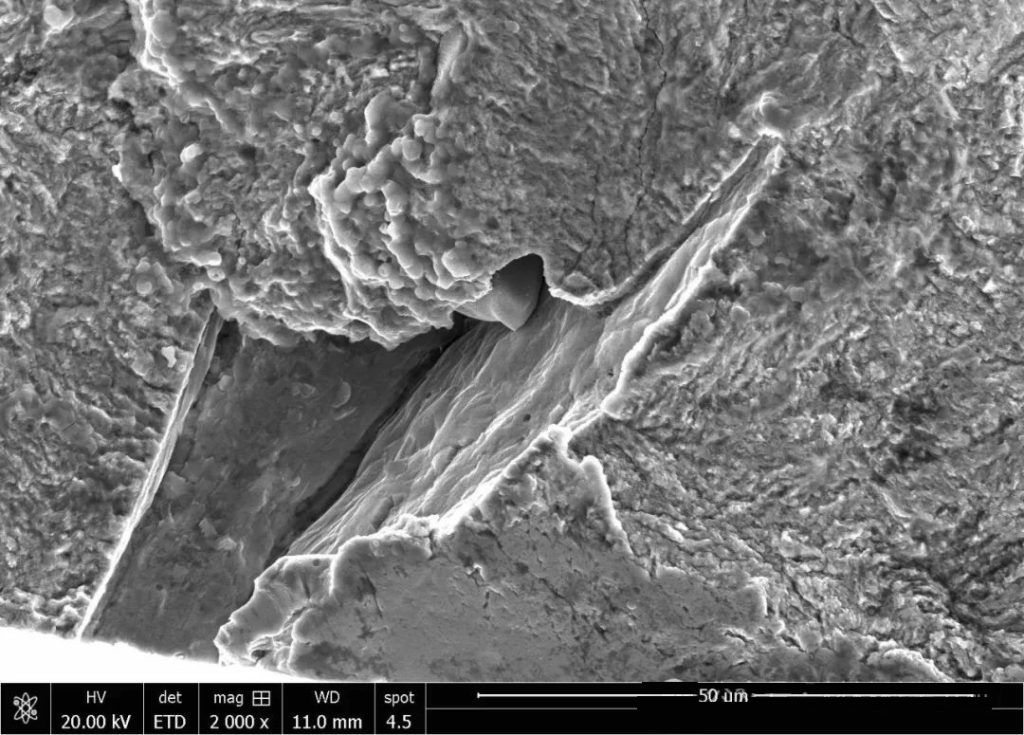
Figure 3
extended area
A magnified view of the extended area shows dense fatigue glow patterns, see Fig. 4.
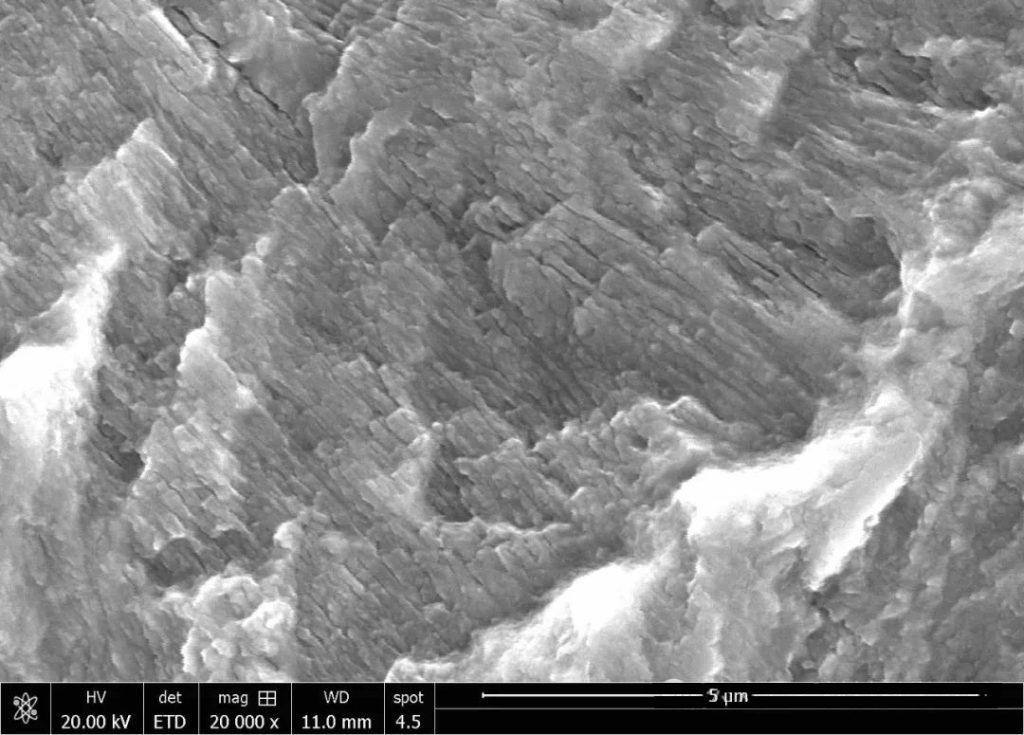
Figure 4
instantaneous zone
The transient break region is characteristic of the ligamentous fossa, which tears and separates in a very short period of time, see Figure 5.
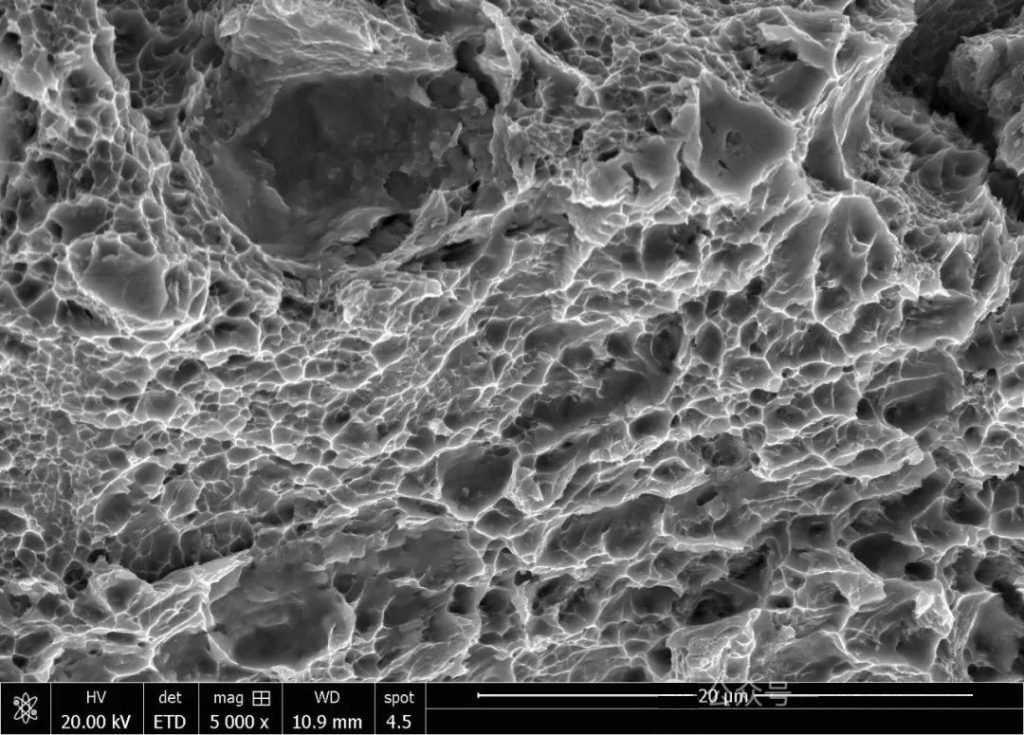
Figure 5
Fatigue failure is often seen in industrial production. Fatigue fracture not only affects the normal use of components, but also causes economic losses and even leads to major safety accidents. Fatigue fracture, generally in the low stress state of the force is not much happened, the accident is often no sign, once found, components or equipment has been scrapped. Therefore, it is of great significance to study the law of fatigue failure of materials.
Conventional research suggests that if a metallic material undergoes ten million cycles of cyclic loading at a certain stress level without failure, then it can be assumed that the material can withstand unlimited operation at that stress level. In practice, however, the actual service life requirements for some high-strength steels, or structural steels subjected to high-frequency, low-stress cyclic loading, exceed this value. In this case, the traditional fatigue test method can not meet the fatigue performance of such materials in the ultra-long life of the study.
The running time before fatigue rupture in practice is long, and experimental studies cannot take a long time to satisfy the long running time. Ultra-high week fatigue can shorten the experimental time and improve the efficiency. With the rapid development of industrial technology, the requirements for the fatigue life of metal components are getting higher and higher. Ultrasonic fatigue test technology, the study of ultra-high circumference fatigue behaviour of metal materials provides a new means, at present, the exploration of ultra-high circumference fatigue behaviour has become a new hotspot for research in fatigue. Of course, there are still many problems that need to be further solved in ultrahigh fatigue test.
- Intensive blood pressure lowering can effectively prevent dementia
- Oxygenation decreases when you move? “Oxygen therapy + exercise” linkage, grasp four key points
- Analysis of Intravascular Ultrasound (IVUS) Design Principles, Assembly Structures, and Imaging FAQs
- Can starving yourself protect your heart? See how intermittent fasting can treat coronary heart disease
- Pulsed-field ablation may reshape atrial fibrillation treatment landscape as NEJM publishes back-to-back head-to-head trials