Toughness fracture
Toughness fracture is generally better plasticity, macroscopically there is obvious plastic deformation, necking is also obvious, the shear lip is wider. Figure 1 shows the ductile fracture at tensile fracture.
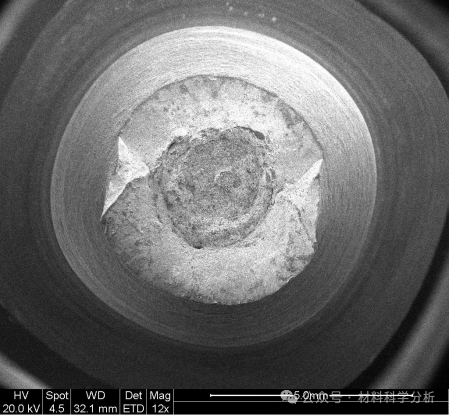
Figure 1
The microscopic morphology of the ductile fracture is characterised by a tough nest, see Figure 2. a tough nest generally has at least one inclusions, precipitates, and other heterogeneous phases. Plastic deformation of the metal is mainly achieved by dislocation slip, slip encounter inclusions or the second phase will be impeded, the formation of dislocation plugging, and in the inclusions – matrix interface to form a concentration of stress, when the stress is large enough, so that inclusions and other heterogeneous phases and the separation of the matrix, which is the generation of microporous. Microporous aggregates grow up, forming tough nests, and then form cracks, and eventually form fracture surfaces.
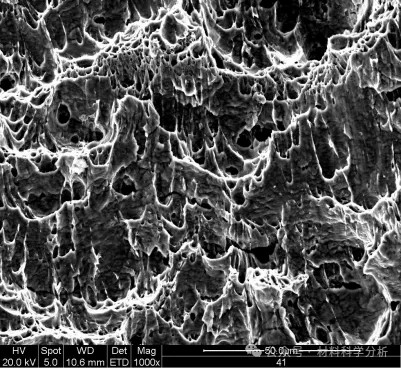
Figure 2
Brittle fracture
Brittle fracture is generally poor plasticity, macroscopic appearance of no obvious plastic deformation, no obvious necking, section flush shear lip is very narrow or no. Figure 3 shows a brittle fracture originating from the surface.
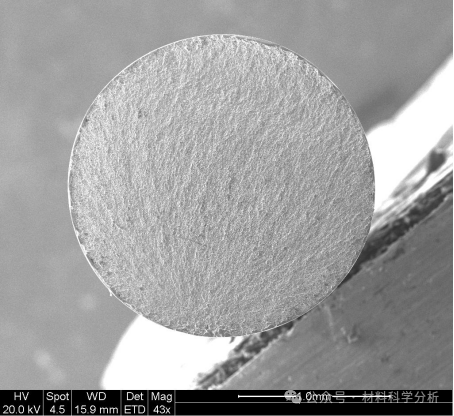
Figure 3
Brittle fractures are characterised by several microscopic features: there are along-crystal fractures, disintegration fractures and fatigue fractures.
Along the crystal fracture is due to the weaker bonding of the grain boundary, the separation occurs along the grain boundary under the action of external force. The reasons for the weakening of grain boundaries are generally the precipitation of brittle second phases at the grain boundaries, or the enrichment of harmful elements, the oxidation of grain boundaries, and the accumulation of gases. The microscopic morphology along the grain is shown in Fig. 4.
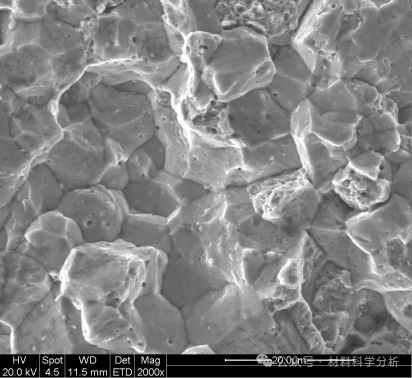
Figure 4
Decomposition fracture occurs along specific crystal faces, generally the more widely spaced faces, because it is easiest to separate along such faces. The body-centred cubic crystal system is generally deconvoluted along the {100} facets, and sometimes also along the {110}, {112}, {111} and other facets. The fracture microstructure is shown in Fig. 5.
Dense-row hexagonal crystals generally undergo deconvolution along {0001}. The face-centred legislative slip system is more frequent, and generally does not occur in deconvoluted fracture.
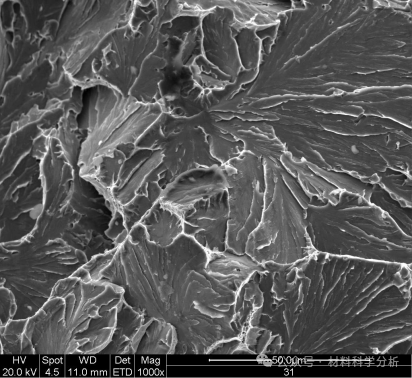
Figure 5
There is another kind of fatigue fracture, also belongs to the low stress brittle fracture. Fatigue fracture macroscopically there is also no large plastic deformation, except in the final instantaneous fracture area is overload fracture, deformation is more obvious. Macroscopically sometimes can also be observed on the shell line. Figure 6 is the macroscopic fracture of fatigue fracture, the obvious shell lines can be seen.
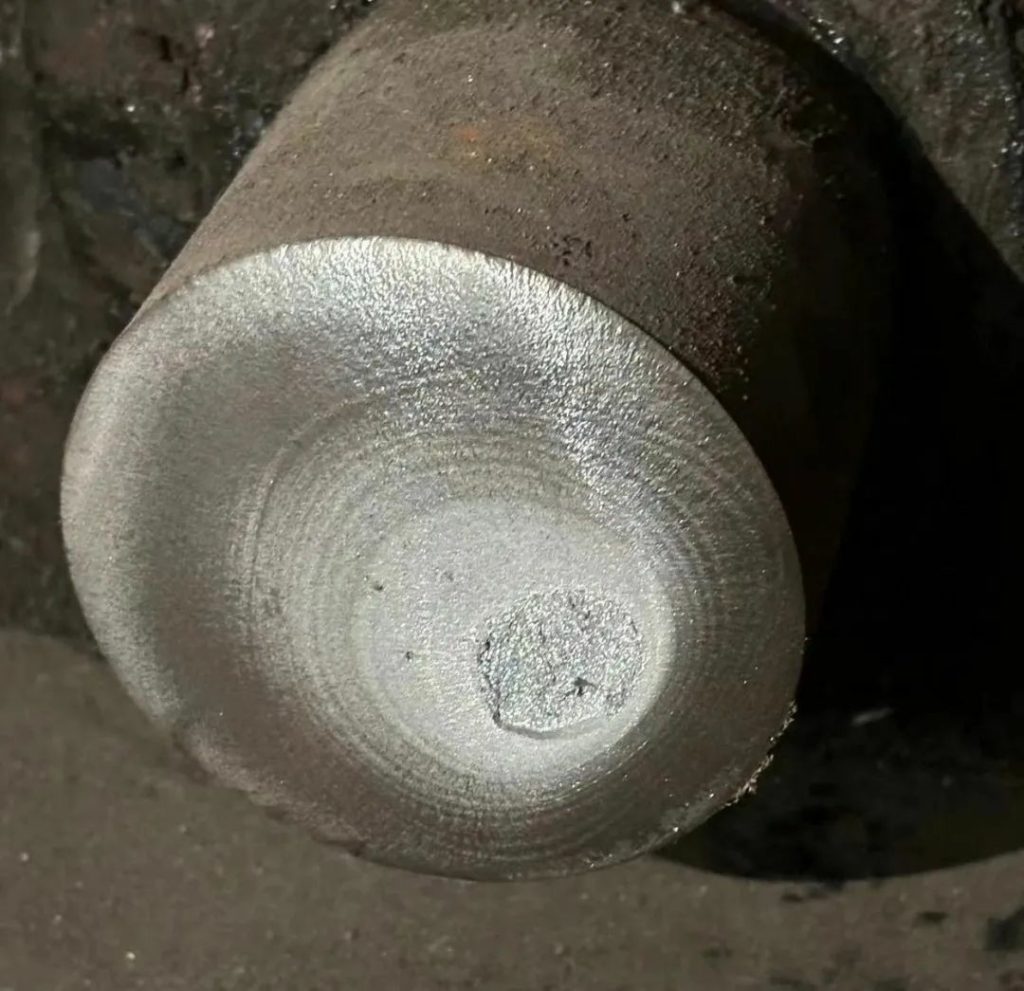
Figure 6
When viewed at higher magnification under a scanning electron microscope, a fatigue glow is visible, see Figure 7.The actual fatigue fracture has different fatigue characteristics depending on the environment and the stresses applied. In some sections, it is difficult to find fatigue glow, but rather extrusion deformation features, or tyre indentation features.
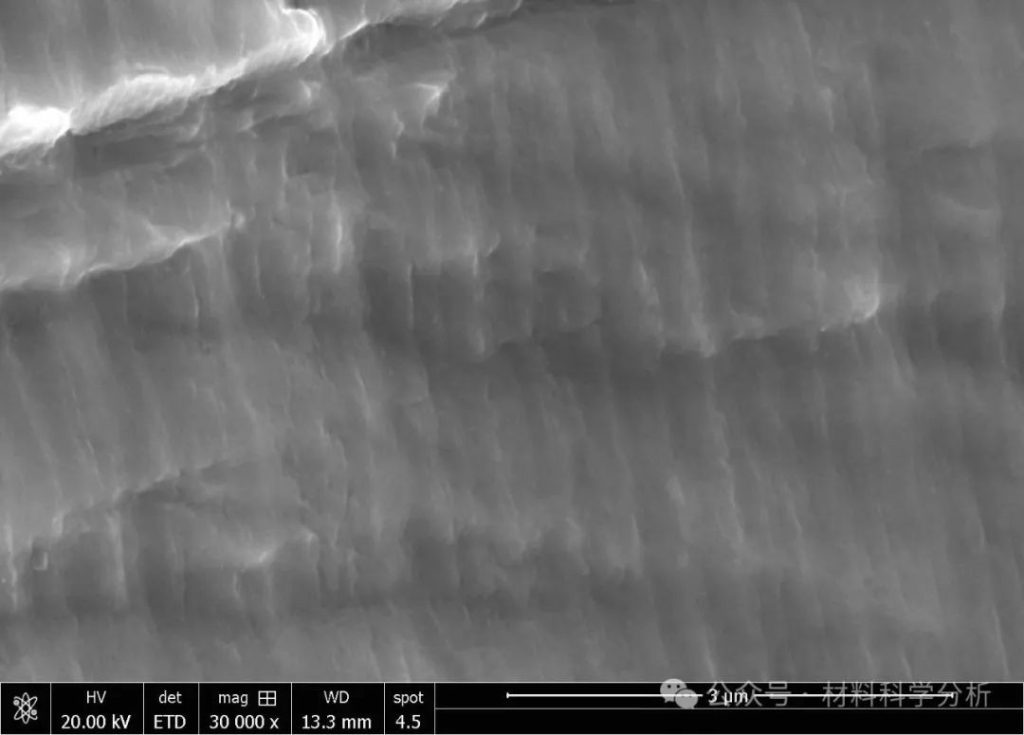
Figure 7
Fracture study is a discipline. According to the fracture characteristics can be deduced from the fracture nature of the material, so as to determine the cause of the fracture, so fracture science in the failure analysis is of great significance.